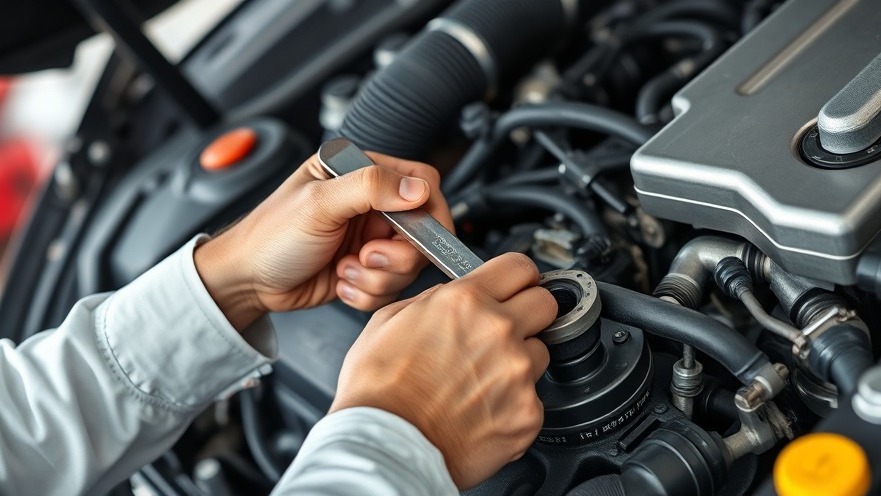
Understanding Technician Productivity: A Deeper Dive
Auto repair shop owners constantly face the challenge of maximizing technician productivity. However, as anyone in the industry knows, productivity isn’t just about the hours logged on a car. While technicians play a pivotal role in meeting performance expectations, the factors influencing their productivity often extend beyond their control.
Efficiency vs. Productivity: Know the Difference
It's important to distinguish between efficiency and productivity. Technician efficiency refers to how well a technician utilizes the time allocated to complete a task, whereas productivity indicates the total time a technician is billing compared to the time spent at the shop. More often than not, a technician might be highly efficient—able to tackle jobs swiftly—but still appear unproductive if they are frequently hindered by prolonged downtimes, such as waiting for parts or encountering workflow disruptions.
Common Causes of Low Technician Productivity
Several factors can detract from technicians’ productivity:
Inaccurate Labor Billing: Many shops struggle with properly estimating the time required for complex jobs. Complications such as rust, seizing bolts, or improperly documented labor times may lead to lost labor dollars, as highlighted in a recent article from research gathered by IMR.
Workflow Disruptions: According to IMR's 2023 survey, issues like finding affordable parts and timely deliveries are top challenges for repair shops today. When technicians are often waiting for parts or information, it stifles their ability to bill hours efficiently.
Technological Proficiency: With vehicles becoming increasingly sophisticated, technicians must continually update their skills and knowledge. A lack of ongoing training can prevent them from staying current with the latest diagnostic equipment and software updates, further hampering productivity.
Improving Production Levels Through Training and Communication
Addressing low productivity starts with understanding workflow. Implementing staff training to improve diagnostic skills can ensure technicians are utilizing the most effective methods to perform their tasks—resulting in a smoother operation that enhances billable labor hours. Moreover, fostering a culture of communication and teamwork ensures that everyone is aligned, allowing for quick problem-solving and efficient work practices.
The Role of Leadership in Technician Productivity
As leaders in the auto repair industry, shop owners must recognize their influence on technician productivity. Setting realistic expectations, ensuring clear communication, and fostering an environment where feedback is encouraged are essential. By addressing barriers to productivity through actionable strategies and appropriate training, shops can empower technicians and enhance overall operational efficiency.
Take Action for Your Shop’s Success
Understanding the complexities of technician productivity goes beyond setting expectations for performance. It involves addressing the nuances of workflow, training, and communication within the shop. As you explore these opportunities, consider investing in thorough training programs that will keep your technicians up-to-date and capable of handling the modern challenges faced in the automotive world. This can lead to increased productivity, customer satisfaction, and ultimately, more profitability for your business.
Write A Comment